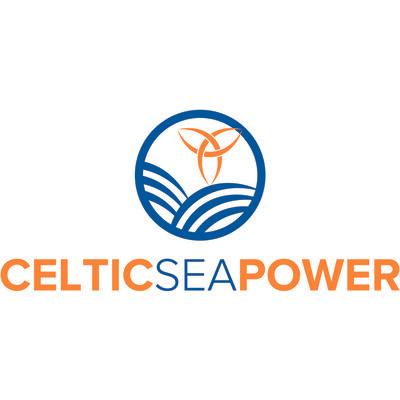
Environmental services are of key importance to offshore wind - especially in the development phase when consenting decisions must be informed by actionable data.
The acquisition and analysis of data on wind, wave, seabed and marine-life is a real strength of the UK. Especially given the vibrant innovation in platforms, sensors and AI.
OWIC's IGP report recognizes this as a priority, noting the UK is already exporting expertise in environmental services. Celtic Sea FLOW offers a particular opportunity, as both a greenfield site and host to a number of companies excelling in this field.
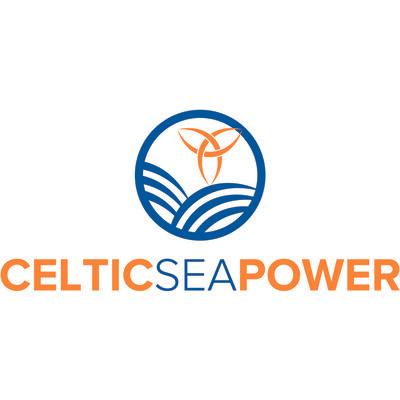
The offshore wind industry faces a range of practical challenges which do not fall into distinct category of opportunity "Logistics” will however be absolutely essential if more fixed and floating turbines is to be deployed and run smoothly at scale.
This is especially so in the Celtic Sea region which lacks mature infrastructure for offshore energy but will require a range of enabling expertise in:
- Haulage eg of aggregates
- Vessels
- Anchor storage
- Crew transfer
- Personnel provision
- Specialist Training
- Cranage
- Draft reduction technologies
- Wet storage
Many of these services are likely to require local know-how and may even provide a strong starting point for ambitious companies to expand into this new market. Not easy to evaluate but there is high potential for regional economic benefit to be derived in logistical and operational services to enable FLOW.
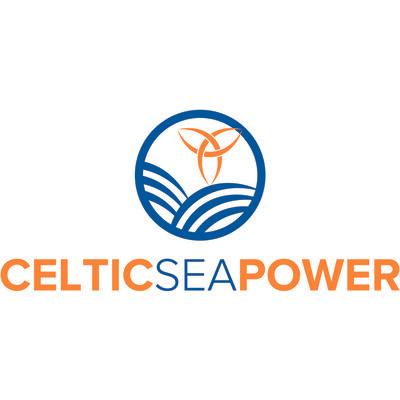
Electrical systems for offshore wind includes array, offshore and onshore export cables, electrical systems and SCADA design.
OWIC's Offshore Wind Industrial Growth Plan has prioritised dynamic cable manufacture for the UK to 'make’. Significant capability exists in the UK but the sheer scale presents a capacity challenge.
Inter-array cables for floating wind in the Celtic Sea alone will require as much as 41km of dynamic and 515km static cables - and require 3-6 cable-laying vessels.
The potential for UK companies to scale-up existing capability is clear. To do so will require close-working with ports and shoreside facilities at an early stage. Major investment is needed (30-50m according to the IGP) and the twin risks, of demand and timing in a speculative market, under-written.
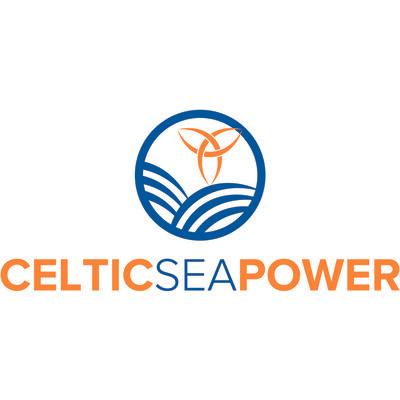
Operations & Maintenance of floating wind (FLOW) will involve the servicing of platforms the height of a sky-scraper many miles out to sea.
Around 260 such platforms are expected to be deployed in the Celtic Sea by the late 2030s. All will require scheduled and unscheduled maintenance of the turbines themselves - but also the towers, floating platforms, cables, moorings and anchors.
Much uncertainty remains on how O+M will be completed for FLOW but it's a clear that a wide range of expertise will be required. Marine operations, remote monitoring, major component replacement, sub-sea inspection, vessels and the logistics to support "next gen O+M" (as highlighted in OWIC's IGP report as an area of high priority opportunity for the UK.
There is much yet to be learned from the few test and demo FLOW sites; but we believe there is scope for developing ambitious approaches to service provision.
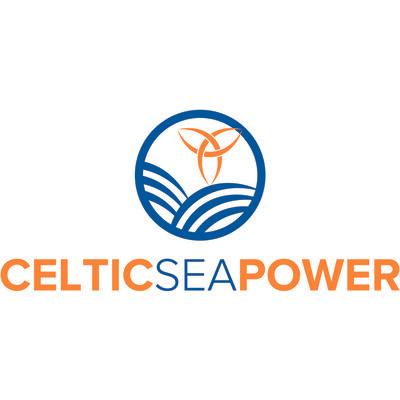
FLOW sub-structures are enormous. The size of a football pitch, ten stories high and weighing up to 20,000 tonnes. Built from either steel and concrete or concrete and secondary steel, sub-structures carry c70% of the cost of the completed unit and c30% of the overall CAPEX.
The UK, and the Celtic Sea region in particular, has significant capability and capacity in concrete and aggregates (demonstrated in the SW by Hinkley-C). Should FLOW opt for a "design-to-local" approach a shorter supply chain has the benefit of resilience for energy security. Delivery from our region would require early investment but derive significant GVA and jobs for the UK.
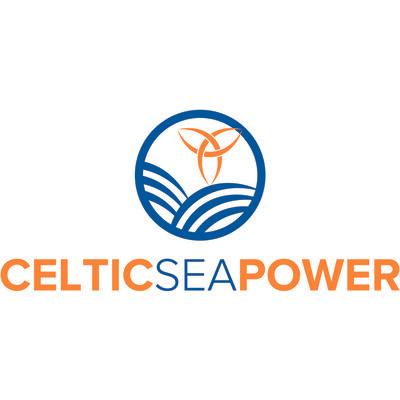
Floating offshore wind (FLOW) platforms must be secured to the seabed - requiring a huge amount of mooring lines, chains and anchors.
The UK FLOW Taskforce "Vision 2050: Anchoring the next generation offshore" identifies A+M as the highest value element to FLOW for the UK economy with "realisable value by 2050 of 6.3bn".
A+M are an area of particular UK strength, notably so in Cornwall, the North East and Scotland. However, key elements remain unknown and the seabed characteristics of the Celtic Sea pose particular challenges. Can solutions local knowledge and UK capacity and ambition can solutions be developed in advance - to realise this potential?